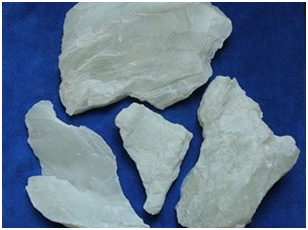

1.Improved
printability:
· It makes the paper smooth and slippery due to which it runs smoothly through the printing process.
· It offers compressibility which ensures maximum ink transfer thereby improving opacity of printing and allowing minimum mottling, smearing or missing dots.
2.Better look and
feel :
· Talc is high in whiteness and thus results in high whiteness of the paper.
· Talc adsorbs the optical brighteners and/or color coatings added to the paper due to which they stay on the surface of the paper, providing maximum effect.
· Its smoothness and slipperiness gives good finish to the paper.
3.Improved strength
and durability:
· Talc offers high paper strength potential which implies that one can load high amounts of the filler with minimum compromise on the final strength of the paper.
· Barrier coatings are often added to the paper to impart durability. Talc minimizes water vapor transmission from the paper, thereby further enhancing the sealing effect of the coatings.
4.Improves efficiency
of the paper making process itself:
· Talc is hydrophobic in nature and therefore permanently absorbs organic particles present in paper pulp called pitch (or stickies, if they are tacky in behaviour) into its molecular layers. Such particles would otherwise adversely impact the paper making process.
· Talc is soft and therefore causes minimum wear and tear of machines through the paper making process.
· Talc improves drainage of water thereby allowing the paper to dry quickly. Further it minimizes loss of other substances during drainage.
· For use in paper industry, pulverized material of 300 BSS sieve is required, which is free from gritty material and contains low levels of CaCO3 and FeO.